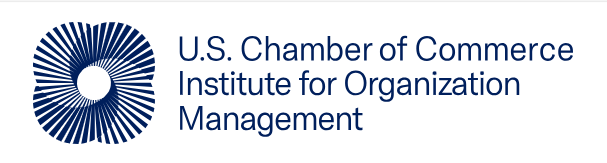
Effective Emergency Response Plans
If current events have taught us one thing it is this: emergencies DO happen. As a result, insurance premiums for many facilities are skyrocketing, the cost of defending against lawsuits is rising, and regulatory agencies are paying closer attention to industries’ preparedness programs. Anticipating emergencies and planning your response can greatly lessen the extent of injuries and limit equipment, material and property damage.
There is no single definition what constitutes an emergency. The word emergency also takes on new meaning depending upon the industry in which you work. A simple water pipe break could spell disaster if you are in the computer business and the break occurs near your servers or PCs. A power outage could spell disaster in the refrigeration industry. High winds could affect your level of customer service in the electric or cellular business. One thing is sure: the degree and effectiveness of preparedness often spell the difference between emergency and disaster. Studies show that organizations with effective Emergency Response Plans suffer losses only 6% of those organizations with ineffective response plans.
Emergency Response Plans (ERP) are also the law. The Occupational Safety & Health Administration (OSHA) requires facilities with over 10 employees to have a written emergency plan. Employers who do not meet OSHA regulations on emergency preparedness are subject to citations and fines.
Your ERP should outline basic preparedness steps needed to handle the anticipated emergencies at your work site. Since your ERP needs to address all emergencies that can reasonably expected to occur in your particular workplace, you need to perform a hazard survey to determine your exposures.
A few items to consider are:
- Do nearby facilities pose a threat?
- What types of natural risks are present?
- Are technological risks accounted for?
- Could civil disorder impact operations?
- Is documentation current for all hazardous materials?
Based upon your hazard assessment, your ERP should then be written for each of the various emergency situations. The basic elements of an ERP are:
- Prevention: this section of an ERP must address your General Prevention Policy; Fire Safety Policy; Safety and Health Reviews and Facility Safety Committee.
- Preparedness: Training; Drills and Exercises; Facilities, Supplies and Equipment; and Public Information must be outlined in detail.
- Response: the “meat” of your ERP is defined here. Items to consider include Emergency Communications; Evacuation and Personal Accountability; Government/Private Agency Coordination and contingencies for each of the hazards uncovered in the hazard survey.
- Recovery: dealing with the aftermath appropriately can greatly reduce the seriousness of future emergencies. Topics to include are: Incident Investigation; Damage Assessment; Cleanup and Restoration Operations.
Ten Most Common ERP Errors
- No upper management support
- Lack of employee buy-in
- Poor or no planning
- Lack of training and practice
- No designated leader
- Failure to keep the plan up-to-date
- No method of communication to alert employees
- OSHA regulations are not a part of the plan
- No procedures for shutting down critical equipment
- Employees are not told what actions to take in an emergency
Throughout development of your ERP remember that its purpose is to provide a safe environment for employees during an emergency and to limit the loss of property. The Boy Scout motto, “Be Prepared” comes to mind. Putting your plan in writing, communicating it to employees and implementing it through regular drills will ultimately pay off when a real disaster occurs.
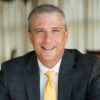
Additional Info
Related Links : https://institute.uschamber.com/effective-emergency-response-plans/?utm_source=sfmc&utm_medium=email&utm_campaign=attribute1&utm_term=12012023_insight